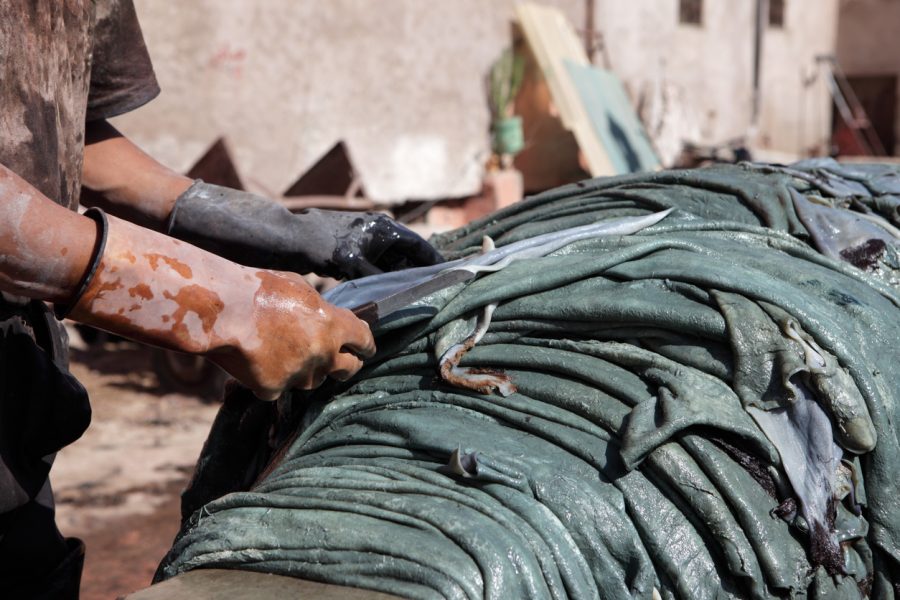
Why tanneries of Bengal’s leather hub predict dark days ahead
With shipments worth over ₹600 crore at stake, business in the Calcutta Leather Complex (CLC), the largest leather cluster in Asia, is unlikely to normalise even after COVID-19 is long gone.
Most tanneries at CLC are lying idle even after the government asked them to resume limited-operation, indicating what lies ahead for one of the most coveted clusters in West Bengal’s Micro, Small and Medium Enterprise (MSME) sector.
A few units in the complex, which are functioning while maintaining COVID-19 safety protocols, are merely processing raw hides they had procured before lockdown to prevent them from rotting, said Zia Nafis, joint secretary of the CLC Tanners Association.
With over 63,215 units, the state accounts for 11.62 per cent of the total MSMEs in the country. There are 531 different clusters in the state at present.
Related news: MSME’s struggle as migrant workers look to leave for home
Some of the other prominent clusters are the fan cluster at Bansdroni and the textile cluster in Metiabruz, both in Kolkata, the zari cluster in Howrah, the belle metal cluster in Bankura and Murshidabad, the handloom cluster in Nadia and East Burdwan and the furniture cluster in the north Bengal districts of Cooch Behar, Alipurduar and Jalpaiguri among others.
The CLC, spread over about 4.5 sq km in Bantala, in the eastern fringe of Kolkata, has so far been regarded as one of the most prospective of all the MSME clusters in the state. It has a current annual turnover of around ₹5,000 crore and houses about 400 tanneries and 60 leather goods manufacturing units.
Less than a year ago, chief minister Mamata Banerjee, while rolling out a red carpet for tanners from Uttar Pradesh, named the complex Karmadiganta (new horizon for job opportunities). As per the government’s estimate, it has the potential to attract an investment of ₹80,000 crore and generate around 5 lakh jobs in a few years, becoming the world’s largest leather hub in the process.
Orders frozen, products rot
But all that was before the coronavirus pandemic hit the world. “The pathogen-infused worldwide lockdown has frozen export orders of almost over ₹ 1100 crore of India’s leather sector alone, a bulk of which was to be executed from Bengal,” said Ramesh Kumar Juneja, regional head, Indian Leather Products Association (ILPA).
Nafis said due to the worldwide lockdown, as per the association’s conservative estimate, orders of processed leather and finished leather products worth at least ₹600 crore have either been put on hold or are in transhipment in the last one-and-half month.
Besides, finished leathers and goods worth several crores of rupees are lying in warehouses, blocking precious ‘capital’ of these small entrepreneurs, creating severe liquidity crunch.
“One of my consignments of a hundred bales of finished leather sheets worth ₹1.5 crore is now lying for over a month at a warehouse in Milan because the importer from Italy is not able to collect it due to the lockdown,” said Ishteyaque Ahmed, owner of the Masooda Impex.
Related news: Need to support MSMEs to tide over COVID crisis: India at BRICS
His another consignment of 32 bales, which was to be sent to Italy, is gathering dust in a warehouse in Mumbai, further constraining his working capital, the exporter said.
Burden of cash crunch, salaries
The situation is not different in other clusters, said Hitangshu Kumar Guha, president of the Federation of Associations of Cottage and Small Industries. He, however, could not cite any estimation of the loss.
“Regular inflow of cash is vital for any MSME that primarily runs on rolling of money,” Guha said, adding that once that flow gets disrupted it becomes very difficult for the small units to churn out their original turnover.
To add to their woes, despite drying up of their cash inflow, the entrepreneurs are having to pay salaries of their employees, minimum electricity bills and rent of their factory sheds among other things.
“My monthly salary burden is ₹90,000 against my nine regular employees. But, now I am paying them only half the salary,” Ahmed said.
“The dilemma before me is even if we resume production, there will be no takers now. I am not even sure how much of the cancelled orders will actually be revived. But even if I get back those orders after the Covid-19 crisis, it will be difficult for me to execute them unless I get at least Rs 15-20 lakh in addition to what little I can shell out from my savings, for procurement of raw materials and chemical” Ahmed added.
Related news: India’s manufacturing sector activity hits record low in April
To address concerns of entrepreneurs such as Ahmed, the Confederation of Indian Industry (CII) has recommended to the government to focus “primarily on increasing the financing available to MSMEs with relaxed collateral norms, an extension of the RBI moratorium and wage support.”
Financial stimulus alone won’t help: MSMEs
To ease the liquidity crisis that most MSMEs are facing due to the lockdown, Assocham has suggested a 40 per cent government or Reserve Bank of India (RBI) guarantee on fresh loans to them.
The Centre’s chief economic adviser Krishnamurthy Subramanian recently announced that the government was planning to release the economic relief package 2.0 soon, which would provide significant liquidity to the MSME sector.
Those involved with the MSMEs, however, feel that the financial stimulus alone will not be enough. They said the government’s directive to run the units with only 15 per cent workforce and the compulsion to maintain adequate social distancing are also putting a spanner on resumption of works in MSMEs.
“Most of these small units run on 1,000 to 2,000 square feet space. Maintaining social distancing is next to impossible there. Moreover, running a unit with only 15-30 per cent of labourers is not economically viable as the production will not be optimum,” Ahmed said.
“The biggest problem is that if the full production is not resumed in another 10 to 15 days, which is rather unlikely, we are doomed,” he added.