- Home
- News
- Premium
- THE FEDERAL SPECIAL
- Analysis
- States
- Perspective
- Videos
- Sports
- Education
- Entertainment
- Elections
- Features
- Health
- Business
- Series
- Bishnoi's Men
- NEET TANGLE
- Economy Series
- Earth Day
- Kashmir’s Frozen Turbulence
- India@75
- The legend of Ramjanmabhoomi
- Liberalisation@30
- How to tame a dragon
- Celebrating biodiversity
- Farm Matters
- 50 days of solitude
- Bringing Migrants Home
- Budget 2020
- Jharkhand Votes
- The Federal Investigates
- The Federal Impact
- Vanishing Sand
- Gandhi @ 150
- Andhra Today
- Field report
- Operation Gulmarg
- Pandemic @1 Mn in India
- The Federal Year-End
- The Zero Year
- Science
- Brand studio
- Newsletter
- Elections 2024
- Events
- Home
- NewsNews
- Analysis
- StatesStates
- PerspectivePerspective
- VideosVideos
- Sports
- Education
- Entertainment
- ElectionsElections
- Features
- Health
- BusinessBusiness
- Premium
- Loading...
Premium - Events
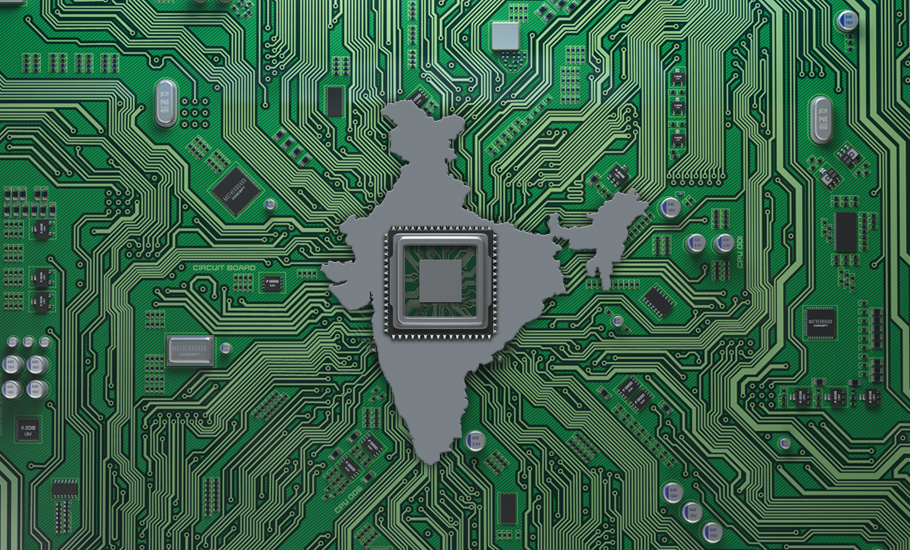
Semiconductor crunch: Why India may have a bargaining chip in future
The widespread knock-on effects of the chip shortage have highlighted how semiconductors have become a foundational technology for the functioning of the modern world.
Several recent developments such as the global chip shortage and geopolitical tensions among key economies such as US-China, China-Taiwan, and Japan-South Korea have turned the spotlight on the semiconductor industry. The global chip shortage, in particular, has somewhat dampened economic recovery from the Covid-19 pandemic for various industries. While the effect of the shortage on the...
Several recent developments such as the global chip shortage and geopolitical tensions among key economies such as US-China, China-Taiwan, and Japan-South Korea have turned the spotlight on the semiconductor industry. The global chip shortage, in particular, has somewhat dampened economic recovery from the Covid-19 pandemic for various industries.
While the effect of the shortage on the auto industry and the ensuing production loss, plant shutdowns and worker layoffs has received significant attention, Goldman Sachs analysts have estimated that as many as 169 end-use industry sectors ranging from consumer appliances to gaming systems and industrial machinery have been affected in some way by the crisis.
The Indian auto industry has also keenly felt the effects of the chip shortage, with a variety of foreign players operating in India as well as domestic players such as Bajaj Auto, Mahindra & Mahindra, Tata Motors and TVS Motors, raising concerns over the impact of the chip shortage on production.
The widespread knock-on effects of the chip shortage have highlighted how semiconductors have become a foundational technology for the functioning of the modern world. Commercially, high volume manufacturing of chips is done only in a handful of countries, with around 78% of the global installed capacity located in Taiwan, South Korea, Japan, and China. In addition, over 90% of manufacturing on leading-edge technology is concentrated in Taiwan.
This lopsided dependence on a few countries for the bulk of the world’s semiconductor needs has become a cause for concern for many policymakers around the world. Many countries such as the United States, European Union and Japan have begun earnest efforts to better understand vulnerabilities in key supply chain nodes, diversify supply chains including sourcing from friendly countries, and boost domestic manufacturing.
Role of India in the semiconductor industry
India has gained a reputation as an important global hub for chip design and product development. Many of the major global players including the likes of Texas Instruments, Intel, AMD and Qualcomm have established R&D centers in India, focusing on design and product development. In addition, a number of homegrown startup-level companies focusing on niche areas have also cropped up in recent years.
Estimates from the Indian Electronics and Semiconductor Association (IESA) value the Indian design services market at $23-29 billion in 2020.
However, in stark contrast to the success India has seen in chip design, it has not developed meaningful capabilities in semiconductor manufacturing and remains 100% import dependent.
While there are small-scale fabrication plants (fabs) and clean rooms operated for captive use by government entities and universities, including the Department of Space, Defense Research and Development Organisation (DRDO), Indian Institute of Science, Bangalore, and Indian Institute of Technology, Mumbai, there are no commercial fabs in India.

Notably, there have been several publicised efforts to start commercial fabs in India in partnership with established global players, including two recent projects in 2016 and 2017 in Uttar Pradesh and Gujarat, respectively. However, they have both been dropped for various reasons and there are currently no major fab projects in the advanced stage of planning or implementation.
Why should India invest in semiconductor manufacturing?
India imported $10.1 billion worth of semiconductor components and micro-assemblies in 2019-2020, with over 70% of the imports from China (via mainland China and Hong Kong). Notably, India’s import for semiconductor components has grown from around $2 billion in 2017-2018 to the current levels, mainly driven by its burgeoning smartphone manufacturing industry, since 2018.
The question of whether India needs to develop capabilities in chip manufacturing is, perhaps, best evaluated within the overall context of its long-term ambitions in key end-use industries. Two important sectors in the Indian industrial scene are ESDM (Electronics Systems and Design Manufacturing) and automotive, both of which are reliant on semiconductors.
India aims to grow its electronics system market to $160 billion by 2025. India is the second largest manufacturer of smartphone units in the world, with major players such as Samsung and contract manufacturer, Foxconn, running operations in India.
While the smartphones produced in India are mostly meant for domestic consumption, with only a small fraction currently being exported, this could be a significant avenue of export growth for the country in the near-to-midterm. India is also seeking to replicate this success in other areas such as tablets, laptops, and consumer appliances.
India also harbors significant ambitions in automotive and electric vehicles, which have higher semiconductor content than internal combustion engine-powered cars. The auto industry contributes to 22% of the manufacturing GDP in India. India is the fourth largest manufacturer in the world in the passenger car segment and has been growing at around 5% CAGR. It also targets to convert 15% of its vehicle fleet to electric vehicles by 2030. Major domestic players including Mahindra & Mahindra and Tata participate in electric vehicle manufacturing in India.
As India seeks to make significant strides in these sectors, a natural concern might be to ensure the long-term robustness of its supply chain, particularly for a key enabling component such as semiconductors, where it remains 100% import dependent. In the case of semiconductors, since developing manufacturing capabilities is a complex, long-term endeavour, India would do well to put in serious efforts into this area now.
Opportunities and challenges ahead for India
Many have pointed out that India’s robust chip design ecosystem as well as the burgeoning electronics industry could lend themselves as captive markets for a semiconductor foundry in India.
In addition, the rapid strides that China has made in adding semiconductor manufacturing capacity has been a cause of concern for the western world, particularly the United States and European Union.
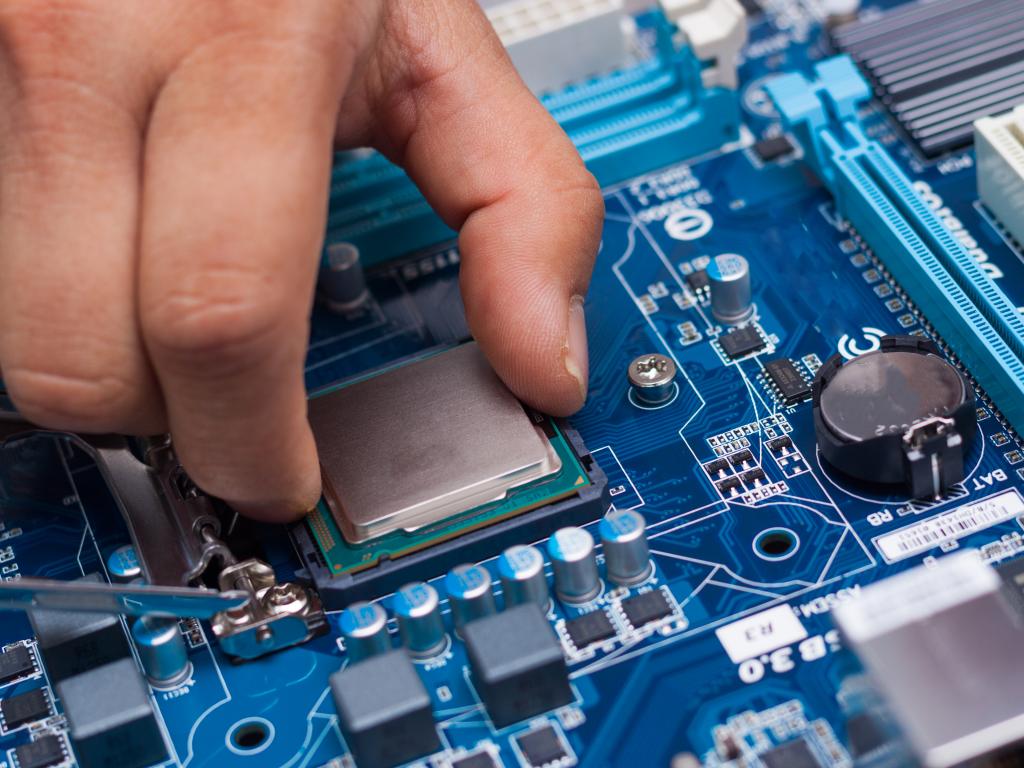
Although a number of global semiconductor companies have invested in manufacturing facilities in China over the years, there continues to be significant uneasiness at the prospect of Chinese dominance in the long-term.
On the other hand, India is largely viewed as a more palatable and friendly partner by the western world. With well thought-out and stable policy strategies, long-term planning, global partnerships, and practical technology choices, there could be a serious opportunity for India to become a respectable force in a period of 15-20 years.
In fact, this situation is not unlike the beginnings of the semiconductor industry in countries such as Taiwan in the wake of concerns over Japanese dominance in manufacturing in the 1980s. Finally, starting a semiconductor fab cluster in India can spawn a secondary industry in construction, consumables supply, parts supply, and so on.
However, there are also significant challenges and potential concerns that should not be minimised. India is a late entrant into the chip manufacturing scene.
Firstly, countries such as China, which are just coming of age in the semiconductor industry, have a 15 year headstart in semiconductor manufacturing experience. Secondly, commercial semiconductor manufacturing is a volume game that is generally cost-effective only when done at scale.
Key characteristics of the semiconductor business include high technology complexity, high capital expenditure, as well as sustained R&D expenditure to keep pace with rapidly evolving technologies. Setting up a new fab can run from $1 billion to upto $20 billion in capital investment, depending on the scale and process technology to be manufactured.
Thirdly, in terms of practical operations, modern chip manufacturing is a highly precise process with little room for error, performed in specially constructed ultraclean environments, requiring significant amounts of uninterrupted power and water supply, as well as a highly skilled workforce of engineers, technicians and engineering managers capable of working in a dynamic environment with attention to detail and agility.
Finally, semiconductor technology is often learnt incrementally generation-over-generation, and leapfrogging technology nodes can be difficult.
Common arguments that one hears for why India cannot do well in the semiconductor industry is the lack of a semiconductor ecosystem and lack of trained human capital.
While true, in some ways, these are also unfair arguments. It is very difficult to develop an effective semiconductor ecosystem and trained human capital cannot be developed in vacuum without concrete efforts in setting up a fab, leading to a chicken-and-egg situation.
Thus, these capabilities have to be developed simultaneously. In terms of human capital, India, in fact, has significant advantages. India has a young and dynamic demographic with a sizeable portion of its student population interested in STEM education.
It is noteworthy that much smaller countries such as Singapore and Israel have managed to place themselves on the semiconductor manufacturing map with fewer resources. In addition, there is a vast diaspora of Indian engineers, engineering managers and executives directly engaged in semiconductor manufacturing around the world, who have nuanced understanding of the industry. Other countries such as Taiwan and China have used this resource very effectively in growing their domestic capabilities.
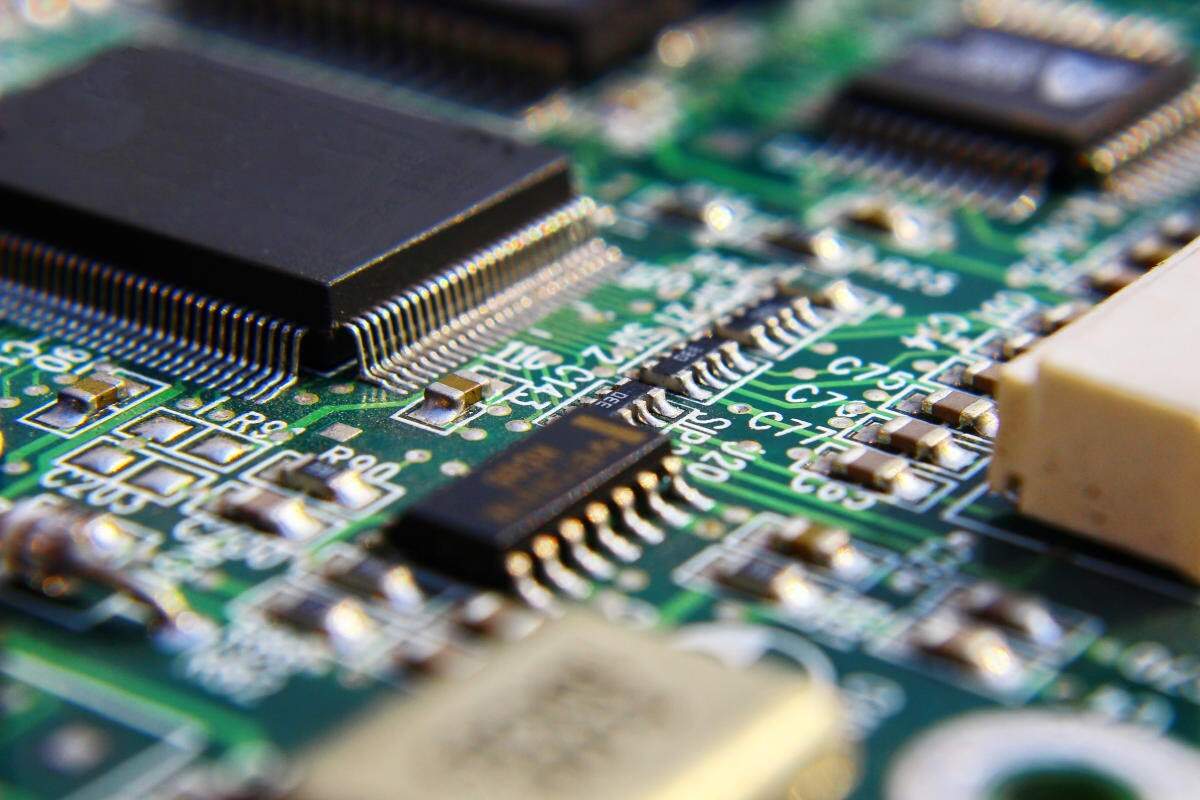
Way forward for India
In its National Electronic Policy 2019, the government of India appears to have recognised the need for developing semiconductor manufacturing capabilities in India as a way to secure the supply chain for key downstream industrial sectors. It has invited proposals for setting up a fab in December 2020. It is reported that over 20 proposals have been received and are under evaluation, with various types of customised incentive plans in consideration.
The practical challenges and barriers in entering the semiconductor industry necessarily imply that, at least during the initial phase of startup and growth, India will need to spread out a red carpet to suitable and established foreign partners, in terms of monetary incentives, coherent and stable policy framework, and resource stability assurances.
India should also carefully study the technology choices for its starting point as it develops the capabilities necessary for running commercial fabs, as well as fit with end-use sectors. While it is not possible or necessary to produce all types of products in demand, some choices could include specialty semiconductor products such as those based on GaN used in optoelectronics applications or trailing-edge silicon-based semiconductors.
A parallel choice for entering the semiconductor industry could be by establishing electronic assembly/packaging and testing facilities (commonly known as OSAT), which have relatively low technology and investment barriers. Initial success in running such ventures could firmly establish India as an attractive destination for foreign investments in this sector.
Finally, semiconductor policy planning in India has to be necessarily done from a long-term standpoint. Realistically, it could take at least three years to start production and achieve reliable yields in a semiconductor fab, even on relatively mature nodes. It could take 10 years to achieve meaningful capability, scale, and develop an adequate pool of talent to successfully run semiconductor fab clusters.
While semiconductor manufacturing will clearly not be a quick success story, unlike the success India has seen with smartphone manufacturing, that also makes it all the more important to start with the best foot forward now, in order to develop long-term capabilities.