- Home
- News
- Premium
- THE FEDERAL SPECIAL
- Analysis
- States
- Perspective
- Videos
- Sports
- Education
- Entertainment
- Elections
- Features
- Health
- Business
- Series
- Bishnoi's Men
- NEET TANGLE
- Economy Series
- Earth Day
- Kashmir’s Frozen Turbulence
- India@75
- The legend of Ramjanmabhoomi
- Liberalisation@30
- How to tame a dragon
- Celebrating biodiversity
- Farm Matters
- 50 days of solitude
- Bringing Migrants Home
- Budget 2020
- Jharkhand Votes
- The Federal Investigates
- The Federal Impact
- Vanishing Sand
- Gandhi @ 150
- Andhra Today
- Field report
- Operation Gulmarg
- Pandemic @1 Mn in India
- The Federal Year-End
- The Zero Year
- Science
- Brand studio
- Newsletter
- Elections 2024
- Events
- Home
- NewsNews
- Analysis
- StatesStates
- PerspectivePerspective
- VideosVideos
- Sports
- Education
- Entertainment
- ElectionsElections
- Features
- Health
- BusinessBusiness
- Premium
- Loading...
Premium - Events
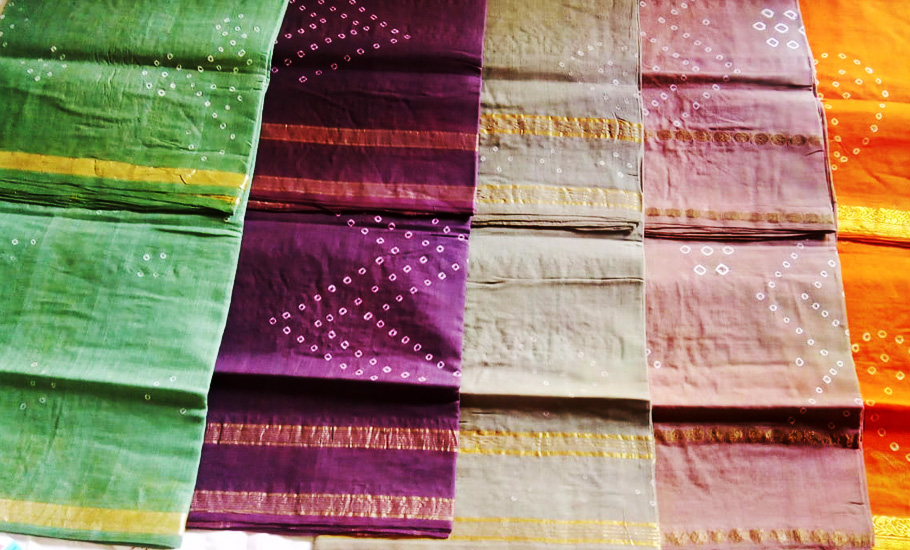
How Saurashtra Tamil Sangamam got wrapped in 6 yards of Sungudi
The fingers move so fast across 6 yards of fabric, it is difficult for even the keenest eye to follow the patterns being woven. The fast moving fingers make thousands of intricate knots on an unbleached handwoven cotton fabric. The knots are spaced evenly and are tightly knit using a thread. So tight are the knots that they remain unshaded during the dyeing and drying process. Even after...
The fingers move so fast across 6 yards of fabric, it is difficult for even the keenest eye to follow the patterns being woven. The fast moving fingers make thousands of intricate knots on an unbleached handwoven cotton fabric. The knots are spaced evenly and are tightly knit using a thread. So tight are the knots that they remain unshaded during the dyeing and drying process.
Even after the dyeing and drying, the fabric in vibrant colours and appealing patterns, appears plain. But they come to life as Sungudi saris once the thread connecting the knots are untied. The tied parts of the sari, which remain unshaded in the original colour of the fabric, give the sari its characteristic, gorgeous Sungudi. The undyed knots look like stars or geometrical white dots of a grand kolam. It is said the craft is creating sungudi saris was inspired by the night sky.
“Just like many other art forms, nature inspired our forefathers to make the first Sungudi sari,” said AK Ramesh, a traditional Sungudi sari maker, who hails from the Saurashtra community living in Madurai. “Just like stars in the sky, the knots are tied in the sari to give it an artistic look. Legend has it that our forefathers were mesmerised by how the stars appeared spread in the canvas-like sky. They tried to recreate the same pattern on a sari and thus invented Sungudi saris,” he told The Federal.
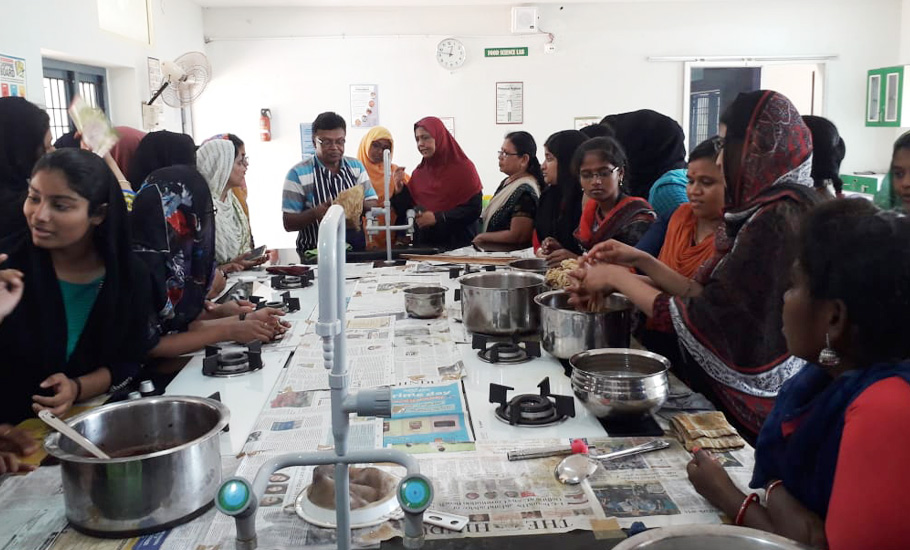
Today, as Gujarat and Tamil Nadu celebrate Saurashtra Tamil Sangamam, under the Union government’s Ek Bharat Shreshtha Bharat programme, the cultural bond shared between the two states stands wrapped in Sungudi saris.
The weavers hailing from present-day Gujarat had settled down in Vijayanagara Empire. It is said during the 16th century due to an economic crisis, weavers from Saurashtra migrated to Tamil Nadu, Kerala, Andhra Pradesh and neighbouring states. Some of them are said to have settled down in ‘Madurai’ on the ‘invitation’ of the Nayaka kings.
Weaving and diamond polishing skills of the people of Saurashtra attracted the Vijayanagara kings without which we wouldn’t have landed up in Madurai making Sungudi saris, said Ramesh.
In Saurashtra, Sungudi comes from the Sanskrit word ‘sunnam’ which means ‘round’, representing the circular dots printed on the fabric as motifs.
When Madurai Sungudi saris got the Geographical Indication or GI tag in 2005, the development was seen a landmark moment, as it recognised more than 700 years of recorded history in the South Tamil Nadu town.
“My quest for an authentic Sungudi sari, handwoven and made using vegetable dye, was fulfilled in Madurai after a search for 10 years,” said 72-year-old Thaila Ananthakrishnan, a resident of Chennai. “I was getting wax printed Sungudi saris. Most of them were made using fabric from power looms. Now, I have nearly 15 Sungudi saris, all of which have been bought from Madurai. All of them are made in the traditional way,” she told The Federal.
The Tamil Nadu prison department as part of reforming and infusing skills for the inmates imparted them training in making Sungudi saris.
The saris made by the inmates were one of the top selling products at the 48th Islands Grounds Exhibition in Chennai, which ended last month. All the saris got sold in just two days, helping the Prison Department get an award for one of the best performing stalls.
When the Madurai Women’s Prison celebrated Women’s Day this year, both the inmates and women officers turned up in Sungudi saris woven by the prisoners.
Luckily, there are those who want to keep this engagement on.
AK Ramesh, who trains people in making Sungudi saris, said he is interested in training inmates in preparing the authentic varieties.
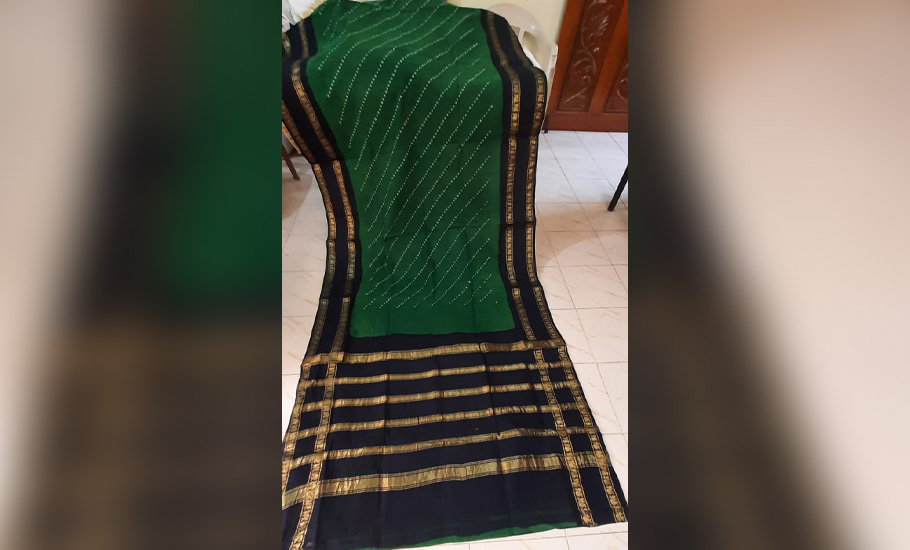
“What the Prison Department has done is commendable. Because making the saris cannot forever remain craftsmanship of the Saurashtrians if the art has to survive. That’s why I train all those who are passionate about it as the art is more important than the business,” Ramesh said.
“Today, we are at trying to save this craft and I don’t want to leave any stone unturned in that pursuit. So, I no longer see it as an art form of the Saurashtra people alone. Instead, I train all those who are passionate about Sungudi saris. When it comes to widows, poor or single women, I train them free of cost,” Ramesh added.
Making Sungudi saris is a time consuming process. It takes 20-25 days to make a single sari in the traditional way as the tying, dyeing and drying involve time. Tying knots itself, an integral part of sari making, takes time. Earlier, people could prepare the same sari in 7-10 days but that is not possible any longer.
“My grandmother spent two days making 20,000 knots. My mother took four days for it. It now takes one month for my wife to do the same work. With distractions like TV channels and mobiles the process gets hit. Also, this cannot be done by hiring people. It is difficult to pay them. That’s why Sungudi weaving has remained largely a family affair. We also involve people who are passionate about it,” said Ramesh who has been training people in making Sungudi saris for the last 10 years.
“Even on days I am tied up, I don’t skip my knitting practice. I practise at least for 30 minutes to one hour. The practice brings perfection to the art,” said Ramesh, who is secretary of the Federation of Tie and Dye Associations, which is working to protect the art.
“Even if we fast pace the production using artificial dyes, it needs at least two days to make one Sungudi sari,” said Ramesh. “But we do it only when a customer asks for it as we focus only on the traditional way of making Sungudi,” he added.
At a time when screen printed saris are sold in the name of Sungudi saris at Rs 400-Rs1,500, it is a challenge to stay afloat protecting the time consuming and labour and cost-intensive traditional sari weaving. Compared to a time when thousands of families were involved in making the saris in Madurai, there are only 40-50 families left today.
Despite authentic Sungudi costing Rs 4,000-Rs50,000, it has a loyal clientele. “Kaikattu (handmade) Sungudi involves rare craftsmanship. So, I don’t mind even if the price is on the higher side. I appreciate the hard work and craftsmanship involved,” said Thaila Ananthakrishnan, who is a retired professor of English from Vellalar College For Women, Erode.
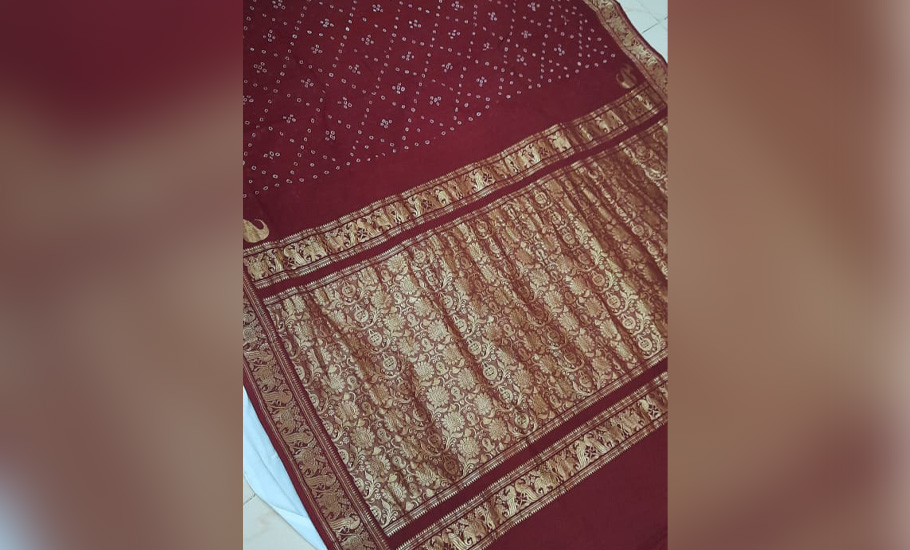
The saris don’t have demand just within India but overseas too. “Natural dyeing for which Madurai weavers are known attracts foreigners. I myself have had 800 foreign customers. Out of them nearly 200 took a three-day course in Sungudi making,” he said. Organisations like the Crafts Council of India are also promoting this craftsmanship by raising awareness and training people.
Even though Sungudi cannot be made in powerloom, it can be made using powerloom fabric and chemical dyes. This helps in bringing down cost and production time but compromises on the art. Some traditional weavers use silk to make the Sungudi saris when their customers make a demand for it.
But many say the comfort of the traditional cotton Sungudi remains unmatched.
“Sungudi is comfortable, cozy and attractive in alluring colours,” said Thaila Ananthakrishnan. “We live in a tropical region and the summers are very harsh. That makes me choose Negamam cotton (made in Pollachi region), Bengal cotton and Sungudi as my favourites. But Sungudi tops the list because of its comfort along with design and colour combination. The saree is so soft. The more you wear it, the softer it gets. For those who want it to remain crisp, starch always helps,” she said.