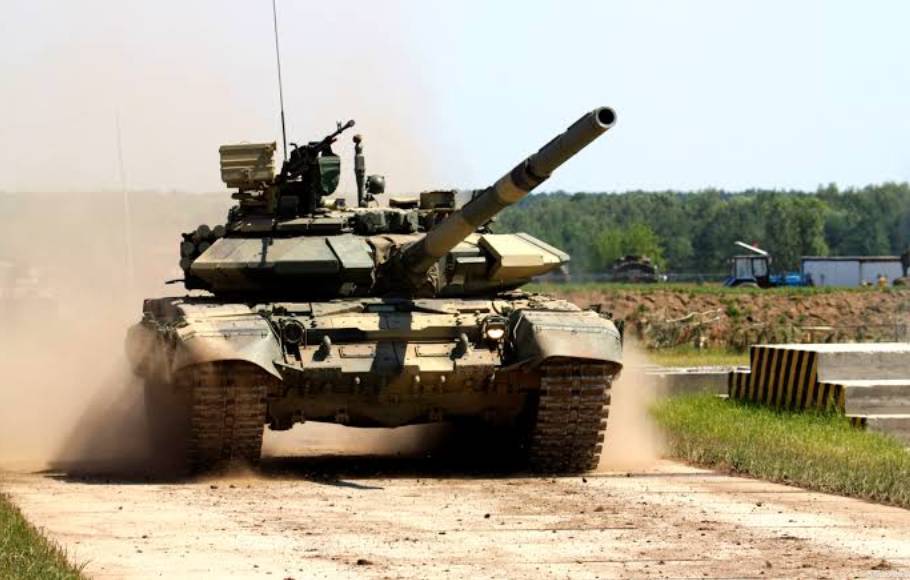
IITK develops strength-enhancing magic potion for Indian army tanks
Fire gun atop the Bhishma tanks a variant of Russian-origin T-90 main-battle tanks of Indian army. As the shell leaves at the breakneck speed of about 5500 km/h, the inner surface of the barrel is eroded. The size of the borehole increases and the accuracy drops.
Boom! Fire gun atop the Bhishma tanks a variant of Russian-origin T-90 main-battle tanks (MBTs) of Indian army. As the shell leaves at the breakneck speed of about 5500 km/h, the inner surface of the barrel is eroded. The size of the borehole increases and the accuracy drops. In battle conditions, with inaccurate guns, the tank and its crew become vulnerable. Scientists from the Indian Institute of Technology Kanpur (IITK) have concocted a new coating to protect gun barrels from wear. Exuberant Dr J. Ramkumar, a member of the research team, says, “Besides, an enhanced life of the gun barrels, these coatings could ensure the safety and longevity of barrels.”
Hail of fire
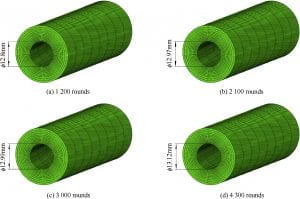
The main gun of the tank is very similar to any firearm. The shell is loaded into the firing chamber. As the fire button is pressed, a large charge is ignited. The blazing combustible propellent releases gas at high pressure and pushes the projectile. The artillery leaves the barrel at high speed and travels in a parabolic path to strike the target.
Hot propellant gases are released when the artillery shells are fired. The temperature of the bore swiftly increases to as high as 1,100 C in a few milliseconds. By the time the cartridge leaves the breech and reaches to muzzle, the temperature rapidly declines to half this value. The top layer of the inner surface of the gun bears the burnt of this abrupt increase and decrease in temperature.
Bore bares the burnt
The rapid surge and drop in the temperature results in two adverse effects. The temperature goes high up and falls down just in 5 to 50 milliseconds. As the fluctuation takes place in a short duration, it does not penetrate deep inside the surface. While at the surface the temperature escalates to 1,000C, at a depth of one millimetre bellow the inner surface, the hike in the heat is just 100 C. In the top layer with a thickness of 200 micrometres, called heat-affected-zone, the microstructure of the steel changes and becomes harder and more brittle.
Secondly, at the high temperatures, carbon monoxide, carbon dioxide, the hydrogen molecule, water vapour, and nitrogen in the air chemically interacts with the inner surface layer of the gun. This further reduces the strength of the steel and makes the surface brittle. The end result of multiple firing, micro-cracks form in the inner surface and the bore diameter increase.
Also read | Researchers at IIIT Hyderabad link music with mental health
Accuracy of the gun
Each gun has a distinct ‘calibre’, that is the diameter of the barrel. The metal projectiles, called as shells must be manufactured with that specification. If the cartridges are smaller than the width of the gun, then there will be gas leakage between the projectile and the worn barrel. If the gas escapes, then the impulse it can impart in the shell will reduce. Further depending upon the direction of the gas released through the barrel, the course of the projectile will also be deflected. In short with the wear of the gun and increase in the bore diameter, the muzzle velocity, range, and accuracy, gradually reduces.
Each time a round is fired, typically the bore diameter increase by about 0.1-200 micrometre. A tank gun may still hit the target reasonably accurate with permissible wear of around 0.5-1% of the bore diameter. For weapons like howitzers, the allowable wear maybe about 5-8% of the bore diameter. Typically after firing about 900 rounds, the barrel of the gun has to be discarded and a new one fitted. Arresting the rate of wear will not only make the barrel last longer but also increase the accuracy of the hit.
Coating to prevent erosion
Conventionally the inner surface of the tank guns is treated with a chemical coating to withstand the temperature fluctuation and reduce the chemical interaction with the steel. Unlike painting the metal rods or walls, the inner surface of the guns is coated with erosion-resistant material using a process called electrodeposition. The barrel is submerged in an electrolyte solution containing the dissolved coating material, when current is applied to the barrel, the suspended particles in the electrolyte solution are activated. The ions migrate towards the metal barrel and deposit on the outer layer.
Hexavalent form of Chromium, called Chromium (VI), is the popularly used coating to improve the barrel’s performance. The catch is, Chromium (VI) is carcinogenic and toxic and at times just peels and falls off the barrel. The trivalent form of Chromium, Chromium (III), is safer and environment-friendly; but hard to use as a coating material. Dr Kantesh Balani, one of the authors, says “due to the complicated chemistry involved in the process, it is difficult to obtain very thick coatings of trivalent chromium compared to hexavalent chromium plating.”
New concoction
In a recent study, researchers from the Indian Institute of Technology Kanpur have created a new blend of Chromium (III) that can serve as a more efficient erosion-resistant coating. They reinforced Chromium with carbon nanotubes (CNTs) and a ceramic compound called yttria stabilised zirconia (YSZ), to improve the properties of the coat. As sugar coating helps to gulp a bitter pill, the new brew worked wonders.
The combination of the carbon nanotubes, which are excellent conductors with Chromium (III) resulted in a thicker layer of Chromium (III), which was a desirable property. The zirconia in the cocktail not only provided the strength to the coat but also prevented the prorogation of the micro cracks. The carbon nanotubes acted like a lubricant reducing the friction of the barrel and the shell and further filled up any cracks that developed. “Incorporating carbon nanotubes make it more resistant to wear, and YSZ reinforcement gives it strength, so we obtain better coatings even at low thickness,” says Pragya Shukla the lead author of the study.
Shikha Awasthi, a co-author of this study, confidently says “There will be a minor increase in cost due to the use of carbon nanotubes and YSZ. But, it would incur much lower costs than for other plating processes both in terms of investment and operating costs, including labour costs.”
Is the concoction a remedy only for the battle guns? No, say the researchers. “It can also be used in rebuilding worn parts such as rolls, moulding dies, cylinder liners and crankshafts,” says Dr Balani.
Also read | IIT grads develop ‘sheet’ that can detect heart disorders, stress when you sleep